Crown Food Europe Download case study pdf
Two new chillers help global packaging producer keep its cool and reduce its energy consumption
Two 155kW packaged industrial chillers were supplied and installed to replace six old units that had become unreliable and inefficient.
Crown Food Europe, WISBECH CAMBRIDGESHIRE.
Part of Crown Holdings Inc., Crown Food Europe is the number one producer of food cans and metal vacuum closures in the world and a leading global supplier of rigid packaging products, transit and protective packaging products, equipment and services to a broad range of end user markets.
Customer Requirements:
When Crown needed to replace the water chillers used to regulate the temperature of one of their key UK production lines, they approached Nexus Cooling. With such a high-speed production line producing millions of cans per year, it’s vital that their machines are cooled efficiently, enabling Crown to maintain the optimum production environment. They also needed to be able to rely on their chillers around the clock, to ensure that production levels can be maintained.
“From the very outset, I had total confidence in the Nexus team and am extremely happy with the installation. In addition to the longer-term cost benefits, which are phenomenal, we’re also seeing additional benefits by no longer having to deal with the breakdowns and maintenance needed on the previous chillers. As far as I’m concerned, Nexus has delivered an outstanding solution, their service levels and response times are second to none, and I wouldn’t hesitate in recommending their services.”
TIM CANNON
Technical Services Manager, Crown Food Europe
Description of chiller package supplied by Nexus
Nexus Cooling’s dedicated engineers installed two 155kW packaged industrial chillers at the Crown site. Under normal operating conditions, each chiller has sufficient capacity to meet the required cooling load, so during scheduled maintenance, or in the unlikely event of a chiller failure, the cooling system will continue to operate, ensuring no production downtime.
Customer progress report
Not only are the chillers reliable but due to their energy efficiency, they’re also contributing to the drive towards Crown’s sustainability targets. The cost benefit of this is also tangible, with Crown estimating that they’re already seeing a 30-35% reduction in energy consumption since moving to the new chillers. In real terms, they predict they’re looking at an 18-month payback, maximum, on the installation.
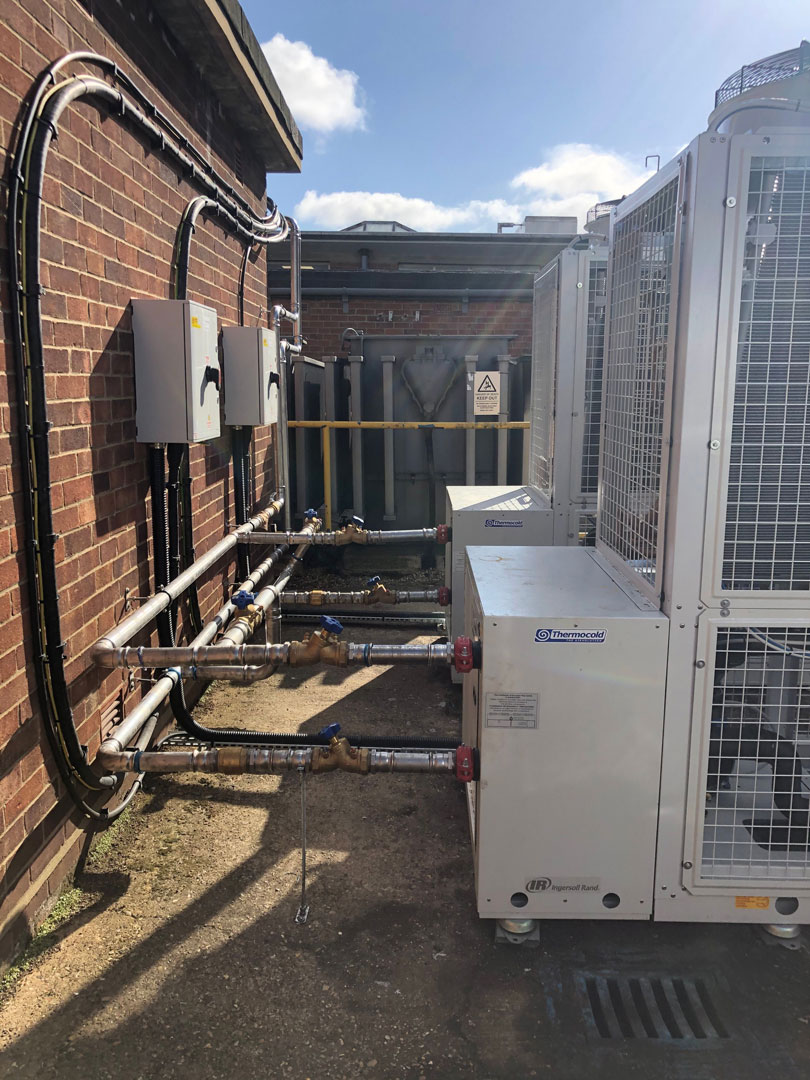